Page 1 of 1
ADC read problem
Posted: Wed Sep 12, 2012 3:15 pm
by GTF
Hello All,
I am working with an 18F14K50. A portion of my program is intended to detect the minimum 10 bit PWM duty cycle required to initiate a position change. I am first reading the pot with the PWM disabled, then continuously re-reading as the PWM is gradually increased. What I have noticed is that if my target is less than .03 to .04V greater than the initial reading, the loop ends on the first pass. There is actually a fair bit of movement required in order to see this much change in the pot output. i.e. the first loop read is already greater than the initial read by at least .02V A meter connected to the circuit does not show any change. I see the same behaviour if I read the ADC as int.
I have attached a short example of what I am doing in this section of the program. Any help is appreciated.
Re: ADC read problem
Posted: Wed Sep 12, 2012 3:38 pm
by Enamul
What I have noticed is that if my target is less than .03 to .04V greater than the initial reading, the loop ends on the first pass.
0.02 v is your condition mentioned in the program 0.03 is greater than 0.02 so program should pass the loop..I might be completely don't understand what you are trying to say..
There is actually a fair bit of movement required in order to see this much change in the pot output.
this small amount of change is not easy to see.
the first loop read is already greater than the initial read by at least .02V A meter connected to the circuit does not show any change.
where is the meter connected and what change you are expecting and what you can't see..
If you use trimmer resistor to tune ADC voltage, you should be able to see initial value and initial + 0.02 V in LCD (if you have any)..so that you can certainly say program works fine or not..
Re: ADC read problem
Posted: Wed Sep 12, 2012 4:28 pm
by GTF
Hello Enamul,
Sorry if my post was confusing. The .02V is just an example of a value that will not work because of this problem. I actually would like to use a value of only .005V or so, but am forced to use a value greater than .03V, which is at least 1 degree of rotation of the mechanism and is clearly visible. Otherwise the loop ends on the first pass, as if the ADC input is already greater than the initial read plus .02V. I am placing the test meter at the input pin of the 18F14K50.
Re: ADC read problem
Posted: Wed Sep 12, 2012 4:33 pm
by Enamul
Hi,
What is the maximum voltage you might need to measure? As for higher resolution like something you are looking for, I think you need to reduce Vref which will provide higher resolution..
For example, Vref=5V reading as INT, resolution is 5V/1023 = 0.00488V but same could be 1.25V/1023 = 0.00122V
Re: ADC read problem
Posted: Wed Sep 12, 2012 5:41 pm
by GTF
The max value is approximately 4.5V. My current Vref/VDD is 4.75V
I have also done the same thing in the reverse direction. In that case the target to end the loop is a value slightly below the initial read, and there seems to be a similar offset occurring. In both cases the first loop read is always some fixed amount greater than the initial read. edit: it is never lower than the initial read
Re: ADC read problem
Posted: Wed Sep 12, 2012 6:03 pm
by Enamul
OK..I will try to sort that using INT read..I guess I can sort that. I will let you know..
Re: ADC read problem
Posted: Thu Sep 13, 2012 1:42 am
by GTF
Here is a new example and video demonstration. This one runs in both directions ( 2 loops). I corrected errors in the earlier example where I did not select "10 bit" duty cycle. My actual project code does not have that error.
This time I added 1 sec of PWM activation at a DC of 600, followed by a 5 second recovery period, prior to each initial read. This was to check if the pot always returns to the same start point. You will see the first one as a fluctuation in the meter reading as soon as the reset switch is pressed. The green LED is flashing while the first loop is running. Then there is another 1 sec of 600 DC and 5 sec recovery during which the red LED is on solid. Then a new initial read is done. Next the red LED should be flashing while the second loop runs. This does not happen. At the end of the program both LEDs are on solid.
You can see that the first loop does not end until the ADC read is almost double the desired .005V above the initial value. Because the second loop does not run at all, it appears that the ADC read on the first pass is interpreted as already more than .005V below the initial reading...... Although on the meter there has been no change.
video:
http://dl.dropbox.com/u/65295456/ADC%20Test.wmv ....allow a minute for the file to load
In this example the second loop will run briefly if I increase delta to .03V rather than .005V. The first loop in this example actually runs with a delta of .005V, but that does not work in my project code.
Thanks
Grant
Re: ADC read problem
Posted: Sat Sep 15, 2012 12:59 am
by GTF
Here is what the 18F14K50 is reporting via USB to serial vs what my meter reads. The int reads of 755, 757, 759, 755 correspond to meter values of 3.490, 3.496, 3.492, 3.490V. The second int neutral read is always greater than the preceding int read even though it is less(and should be) on the meter.
Re: ADC read problem
Posted: Sat Sep 15, 2012 1:34 am
by Enamul
I see..
I will check in hardware to replicate the situation
Re: ADC read problem
Posted: Sat Sep 15, 2012 4:55 am
by GTF
Here is the problem. The calibrated minimum Duty Cycle for 1 direction ends up too low (and possibly too high the other direction).

I have attached the Flowcode I used for this experiment.
Edit: added some comments to the flowchart
Re: ADC read problem
Posted: Sat Sep 15, 2012 4:02 pm
by GTF
More odd behaviour......
If I disable the second read of the neutral position it is the first minimum duty cycle determination that does not work correctly. Although the targeted position change is reported, there was no change in voltage on the meter, no movement and no PWM applied.
In this case the disabled section of the flowchart does not occur until after the section that does not function correctly!
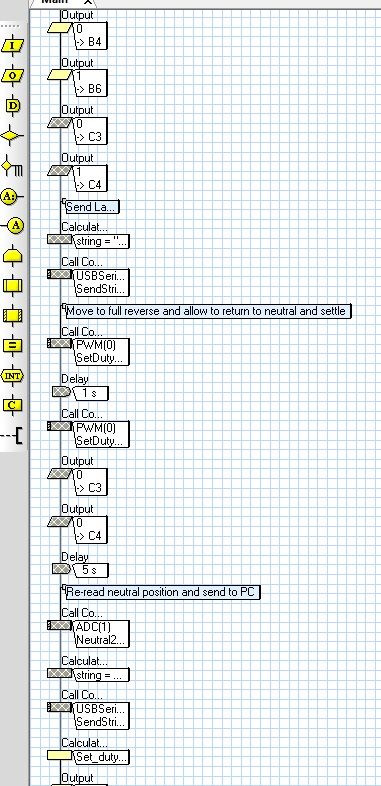
Re: ADC read problem
Posted: Sun Sep 16, 2012 9:35 am
by zadah
Have you tried filtering capacitor on input pin of the PIC?
How about different potentiometer with lower resistance?
Re: ADC read problem
Posted: Sun Sep 16, 2012 4:26 pm
by GTF
zadah wrote:Have you tried filtering capacitor on input pin of the PIC?
How about different potentiometer with lower resistance?
There is a 470nf cap and a 100k pulldown on the circuit. The pot is already proven with other controllers/firmware.
I have also tried multiple samples/averaging with the same results. My impression is that the values being used in the calculations can be off by multiple times the theoretical ADC resolution. So for example, the current position can be determined to be on the opposite side of the stored neutral position than it actually is, requiring the use of a wider than acceptable deadzone.
The stored values appear to be consistent when read back multiple times, so perhaps the problem is inconsistency in the ADC conversion.
Re: ADC read problem
Posted: Mon Sep 17, 2012 3:06 am
by GTF
Although further testing is required to confirm desired operation, it seems my CPU clock speed was low.